Commercial Flat Roofing: Solutions for Manchester Businesses
Comprehensive guide to flat roofing systems for commercial properties in Greater Manchester
Commercial flat roofing presents unique challenges that go far beyond residential work. Manchester’s diverse business landscape – from Victorian mill conversions to modern office complexes – requires roofing solutions that balance performance, cost-effectiveness, and minimal business disruption. After two decades serving Manchester’s commercial sector, we understand that your roof isn’t just about weather protection – it’s about keeping your business operational.
Why Commercial Flat Roofing Differs
Scale and Complexity
Commercial roofing operates on an entirely different scale:
- Larger surface areas (often 1,000m² to 10,000m²+)
- Complex drainage systems with multiple outlets
- Penetrations for HVAC, utilities, and access equipment
- Load-bearing requirements for plant equipment and foot traffic
- Fire safety compliance with strict building regulations
Business Impact Considerations
Unlike residential work, commercial roofing affects:
- Daily operations and revenue generation
- Employee safety and productivity
- Customer experience and brand reputation
- Insurance compliance and risk management
- Regulatory requirements for different business types
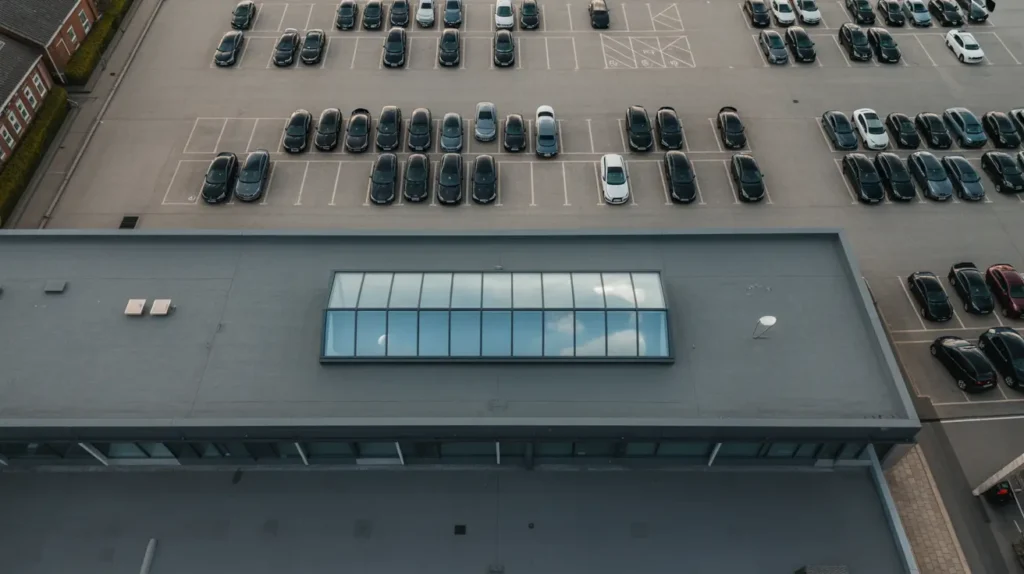
Commercial Flat Roofing Systems
Single Ply Membranes
EPDM (Ethylene Propylene Diene Monomer) Manchester’s most popular commercial choice due to:
- Excellent weather resistance in our variable climate
- 25-30 year lifespan with proper maintenance
- Cost-effective installation for large areas
- Flexibility accommodating building movement
- Proven track record in industrial environments
Typical applications: Warehouses, retail units, light industrial buildings
TPO (Thermoplastic Olefin) Growing in popularity for:
- Heat-weldable seams creating permanent bonds
- White surface reducing cooling costs
- Chemical resistance suitable for industrial environments
- Recyclable material supporting sustainability goals
Typical applications: Modern office buildings, retail parks, food processing facilities
PVC Single Ply Premium option offering:
- Superior durability (30-40 year lifespan)
- Excellent fire resistance meeting stringent safety standards
- Chemical and UV resistance for harsh environments
- Hot-air welding for reliable seam integrity
Typical applications: Hospitals, schools, high-specification office buildings
Built-Up Roofing (BUR)
Traditional Felt Systems
Still relevant for:
- Heritage building compliance in conservation areas
- Cost-sensitive projects requiring proven solutions
- Phased replacement programmes
- Repair compatibility with existing systems
Modified Bitumen
Enhanced performance through:
- Improved flexibility reducing cracking
- Better temperature resistance for Manchester’s climate
- Enhanced puncture resistance for high-traffic areas
- Torch-applied installation for reliable bonding
Liquid Applied Systems
Polyurethane Coatings
Ideal for:
- Complex roof geometries with multiple penetrations
- Refurbishment projects over existing surfaces
- Seamless application eliminating weak points
- Minimal disruption installation processes
GRP (Glass Reinforced Polyester)
Excellent for:
- High-durability requirements (40+ year lifespan)
- Extreme weather resistance
- Walkable surfaces for maintenance access
- Bespoke detailing around complex features
System Selection Criteria
Building Type Considerations
Retail and Hospitality
- Minimal disruption during installation
- Aesthetic considerations for visible areas
- Quick installation to reduce revenue loss
- Low maintenance requirements
Industrial and Manufacturing
- Chemical resistance for process emissions
- Load-bearing capacity for equipment
- Puncture resistance for high-traffic areas
- Fire safety compliance for hazardous processes
Office and Professional Services
- Thermal performance for energy efficiency
- Quiet installation to maintain productivity
- Professional appearance for corporate image
- Long-term value and warranty protection
Environmental Factors
Manchester’s Climate Challenges
- High rainfall (average 806mm annually)
- Frequent freeze-thaw cycles
- Strong winds from Pennine exposure
- UV exposure during summer months
- Pollution from urban environment
Drainage Design
Critical for Manchester’s wet climate:
- Minimum 1:60 falls to outlets
- Adequate outlet sizing (100mm minimum)
- Emergency overflow provision
- Leaf guards and debris filters
- Regular maintenance access
Installation Considerations
Minimising Business Disruption
Phased Installation
- Section-by-section replacement
- Temporary protection systems
- Off-hours working when possible
- Weather-dependent scheduling
Noise Management
- Quiet installation methods where possible
- Advance notification to occupants
- Coordination with business operations
- Sound barriers for sensitive areas
Access Planning
- Crane positioning and safety zones
- Material storage and logistics
- Staff and customer safety measures
- Emergency access maintenance
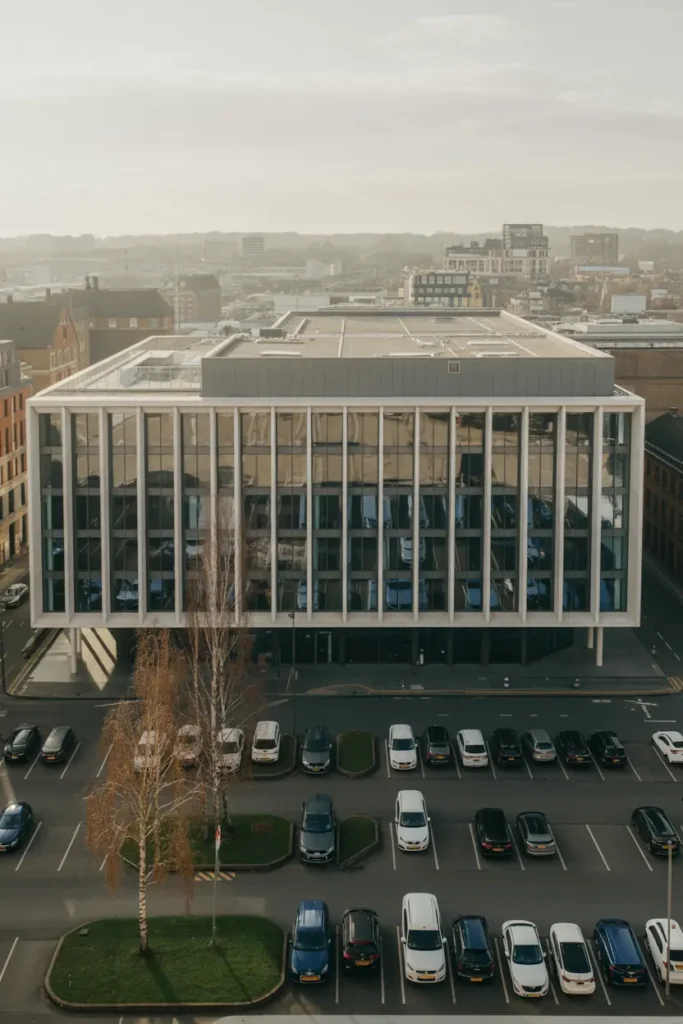
Health and Safety Compliance
CDM Regulations
All commercial projects require:
- Principal contractor appointment
- Risk assessment and method statements
- Competent person supervision
- Worker safety training and certification
Working at Height
- Edge protection systems
- Safety harness requirements
- Rescue procedures planning
- Equipment inspection schedules
Maintenance and Lifecycle Management
Planned Maintenance Programmes
Annual Inspections
Professional assessment covering:
- Membrane condition and wear patterns
- Seam integrity and potential failures
- Drainage system functionality
- Penetration sealing around services
- Structural loading assessment
Seasonal Maintenance
- Spring: Post-winter damage assessment
- Summer: Preparation for heavy rainfall
- Autumn: Leaf clearance and gutter cleaning
- Winter: Ice prevention and emergency response
Predictive Maintenance
Condition Monitoring
- Thermal imaging surveys
- Moisture detection systems
- Structural movement monitoring
- Proactive repair scheduling
Lifecycle Planning
- Replacement timing optimisation
- Budget forecasting for major works
- Performance tracking and reporting
- Warranty management and claims
Compliance and Regulatory Requirements
Building Regulations
Part B (Fire Safety)
- Surface spread classifications
- Structural fire resistance requirements
- Escape route protection
- Compartmentation maintenance
Part L (Energy Efficiency)
- Thermal performance standards
- Insulation continuity requirements
- Thermal bridging elimination
- Energy assessment compliance
Planning Considerations
Permitted Development
- 40% rule for industrial buildings
- Height restrictions in conservation areas
- Neighbour consultation requirements
- Environmental impact assessments
Listed Buildings
- Conservation officer consultation
- Traditional materials requirements
- Specialist techniques and approvals
- Heritage impact assessments
Cost Analysis and Budgeting
Initial Investment Ranges
System Costs (per m², materials and installation):
- EPDM: £45-65
- TPO: £50-70
- PVC: £55-80
- Modified bitumen: £35-50
- Liquid applied: £40-90
Additional Factors
- Access equipment: £5-15 per m²
- Insulation upgrades: £10-25 per m²
- Drainage modifications: £500-2,000 per outlet
- Structural works: Variable, requires assessment
Lifecycle Cost Analysis
20-Year Comparison
- Premium systems (PVC/GRP): Lower total cost through longevity
- Standard systems (EPDM): Balanced performance and cost
- Budget systems (Modified bitumen): Higher maintenance costs
Operating Cost Factors
- Energy efficiency improvements
- Maintenance frequency and costs
- Insurance premium impacts
- Business disruption minimisation
Choosing the Right Contractor
Essential Qualifications
Industry Certifications
- NFRC membership (National Federation of Roofing Contractors)
- Manufacturer training and approvals
- Health and safety accreditation
- Quality assurance systems (ISO 9001)
Commercial Experience
- Portfolio of similar projects
- Reference clients in your sector
- Local knowledge of Manchester regulations
- Emergency response capabilities
Tender Considerations
Evaluation Criteria
- Technical competence and methodology
- Programme and phasing proposals
- Health and safety approach
- Warranty and aftercare provision
- Value for money rather than lowest price
Contract Terms
- Performance bonds and insurance
- Variation procedures and pricing
- Completion timescales and penalties
- Defects liability periods
Future-Proofing Your Investment
Emerging Technologies
Smart Roofing Systems
- Sensor integration for condition monitoring
- Weather station connectivity
- Predictive maintenance algorithms
- Remote monitoring capabilities
Sustainability Enhancements
- Solar integration opportunities
- Rainwater harvesting systems
- Green roof hybrid solutions
- Carbon footprint reduction
Climate Adaptation
Resilience Planning
- Extreme weather preparation
- Flood resistance measures
- Heat island mitigation
- Biodiversity enhancement
Conclusion
Commercial flat roofing for Manchester businesses requires a strategic approach that balances immediate needs with long-term value. Success depends on selecting the right system for your specific requirements, working with qualified professionals, and implementing proper maintenance programmes.
The key to successful commercial roofing lies in understanding that this is not just a building component – it’s a business asset that affects operations, costs, and risk management. Investment in quality systems and professional installation pays dividends through reduced disruption, lower maintenance costs, and enhanced building performance.
For Manchester businesses, the combination of our challenging climate, diverse building stock, and stringent regulations makes expert guidance essential. Whether you’re planning new construction, major refurbishment, or emergency repairs, the right roofing solution protects both your building and your business.